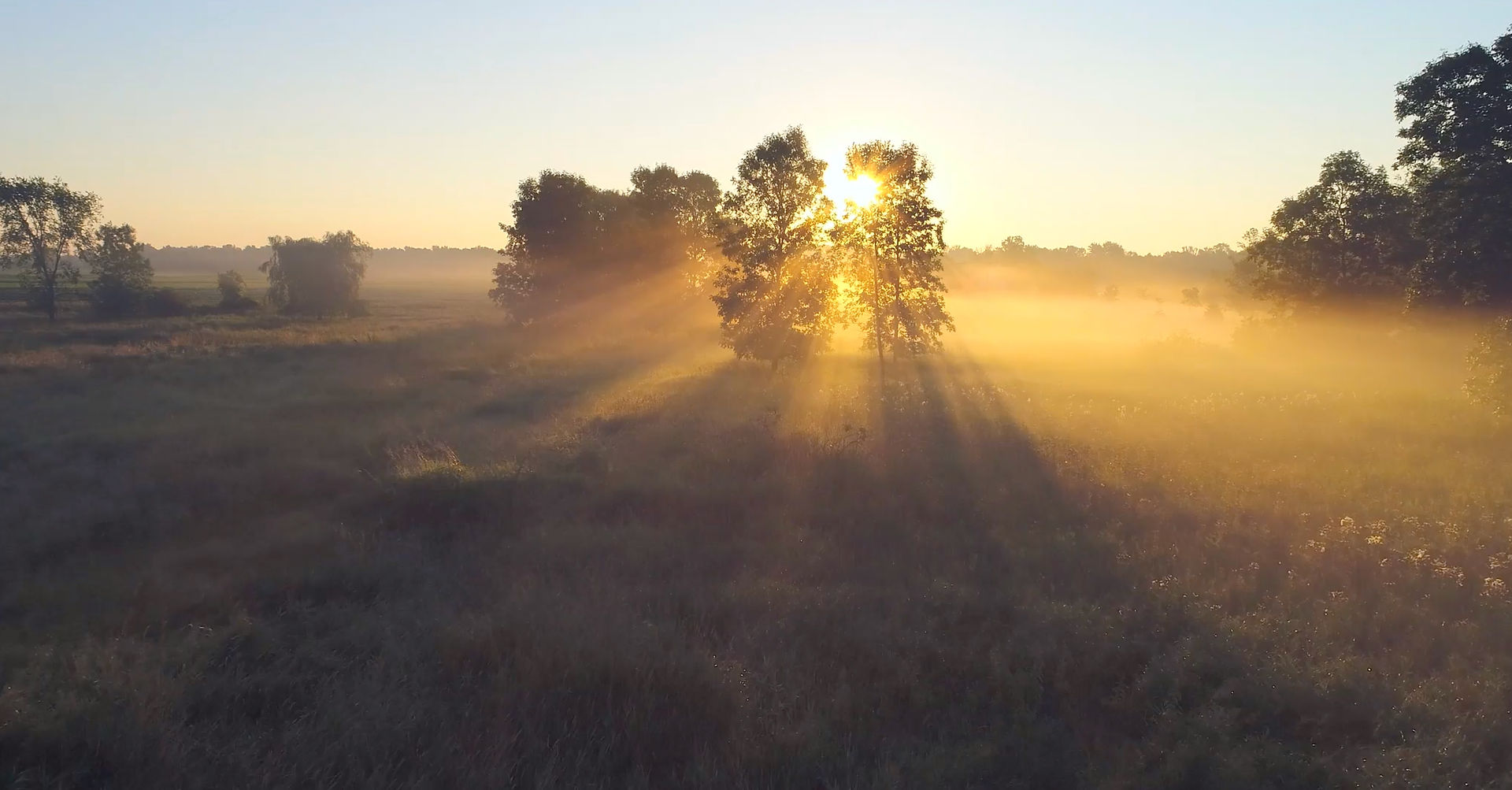

Bright AM Key Results
​
Bright AM™ has some excellent features, functions and benefits, and we can talk about those all day; but if you don’t see positive RESULTS within your own business and production operations, then what’s the point? So, let’s focus on RESULTS. The following list delineates some of the Key Results that
Bright AM™ users have communicated back to us.
Additive Manufacturing Requirements: “After looking at different software solutions for months, Bluestreak Bright AM was the only MES/QMS package that could handle the requirements of our AM production flow."
Raw Material Usage and Advanced Dispositioning: "We also needed better management of nonconformance and scrap parts, and Bright AM gave us the advanced dispositioning and real time control of 3D printed parts that we were looking for."
[Learn More: Additive Manufacturing Materials for Production]
Mobility: “What sealed the deal for us is that all of the Bright AM modules and our key information is accessible anytime, anywhere and on any device, 24x7x365; and we don’t need to manage software on all those devices.” (iMobile Module)
Intelligent Part Planning: “ The Bluestreak system allows us to build a sophisticated process for a new work order on the fly and be able to update a customer part process directly from the work order, which saves us an enormous amount of time."
(intelliPlan Module)
Disconnected Silos of Data: “With the baseline Bright AM package we can now manage customer data and contacts better, quote and price orders, enter work orders and create job travelers, generate Certs, cut Shippers, invoice and manage A/R, and we are almost running completely paperless now." (Quote to Invoice – Q2I base Module)
Scheduling: “We have full schedule visibility by day, week or month; it handles multiple pieces of equipment, and they are color coded to easily distinguish between the schedules.” (Schedule Module)
Job Tracking: “ It has improved our overall quality and reduced our re-work because we can now tie quality management initiatives directly to individual equipment operators on the production floor.” (Production Pathway Module)
Integrated Quality: “Bright AM lets us set up quality control plans that can be attached to an Order that defines the necessary quality and processing requirements. We can include operating instructions, inspection and testing requirements for our Lab, and collect quality data in real-time." (Quality Hub)
Risk Analysis: “When we upgraded from ISO 9001:2008 to 2015 one of the new requirements was to be able to complete a Risk Analysis, so we were pleasantly surprised that Bluestreak had already added that functionality to the system." (Risk Analysis Module)
Safety and Compliance: “With Bluestreak we can store employee information, including their picture and individual training requirements for both safety and production training. And, all safety program documents or OSHA/EPA requirements can be stored right in the system for quick access.”
Underwriters Laboratories, the global safety consulting and certification firm responsible for studies into the safety of desktop 3D printing, has opened online access to all of its library of UL Safety Standards.
SPC: “Our Quality Manager was so excited when he found that the Statistical Process Control feature in Bluestreak Bright AM was able to take Control Plan Characteristics to the next level. We found that any Control Plan Characteristic could be configured for SPC, and that when test results are added, the SPC chart is updated in real-time allowing us to see and be notified at the time of test entry if there are any issues with our process." (Statistical Process Control Module)
Inventory Control: “We can now link inventory items to a specific Vendor and/or vendor part; more easily manage multiple suppliers and multiple inventory locations." (Inventory & P.O. Module)
Shipping and Delivery: “Our shipping department and delivery drivers needed a faster and more accurate way to manage delivering completed parts to our customers, and Bluestreak™ has given us this capability, and we even use smart phones and tablets." (iDeliver Module)
Maintenance: “ A huge benefit is that now our maintenance can be tied directly to production, equipment specifications and job scheduling.” (iMaintain Module)
User Viewing Restrictions: “ Since implementing this software, we can manage and control sensitive information, limit distribution to safe recipients, with traceable communication and easy-to-access audit trails. We can also more easily enforce Classification.” (ITAR/EAR – User Viewing Restrictions Module)
Managing to Industry & Customer Specifications: “ It really simplifies our job processing by linking Quotes and Work Orders to the current specification requirements.” (Advanced Specifications Manager Module)
The Rounding and Converted Units Problem: “ Prior to Bluestreak, the conversion from the Measured to the Reported was done manually, using the appropriate conversion table, and was filled with errors. Now, my Converted Units can be combined with pre-set Rounding Algorithms within the software for all my variable-type Control Plan Characteristics." (Advanced Specifications Manager Module)
Charting Systems: “ We can produce charts for a specific start and end time on a piece of equipment and then save the chart, along with notes and order information that may have been added to the chart.” (BlueCharts Module)
Document Management: “ With BlueDocs we can now track and show revision control with our key documents which is required by ISO and AS 9100." (BlueDocs Module )
Control Plans / Sampling Plans: “We were looking for a software system for our shop floor that would allow us to have a work order or job traveler with part-specific control plans attached to it and are so glad we came across your software."
(Advanced Control Plans / Sampling Plans Module)
Customer Service: “ Our customers can now self-serve 24x7 and don’t need to call us and be put on hold while someone tracks down their information, and it saved our people about 4 hours a day of being on the phone to answer customer questions that they now can get for themselves quicker.” (Customer Connector Module)
ERP Integration: “ With Bluestreak™ we now have bidirectional communication between systems and we can capture any kind of production data during job tracking as well as let the ERP system know when a job is completed”.
Integration with Customer ERP System: Because Bluestreak™ can interface with your customer’s ERP system, you no longer need to enter work orders manually for that customer. When a job is entered into their ERP system it communicates with Bluestreak and generates a custom work order. This eliminates extra steps, human intervention and data entry errors.
Real-Time Communications: “ Bluestreak Bright AM™ pushes real-time notifications through text messaging or email of relevant job functions or triggering events that may occur from time to time." (Global Communications Hub)
​
​