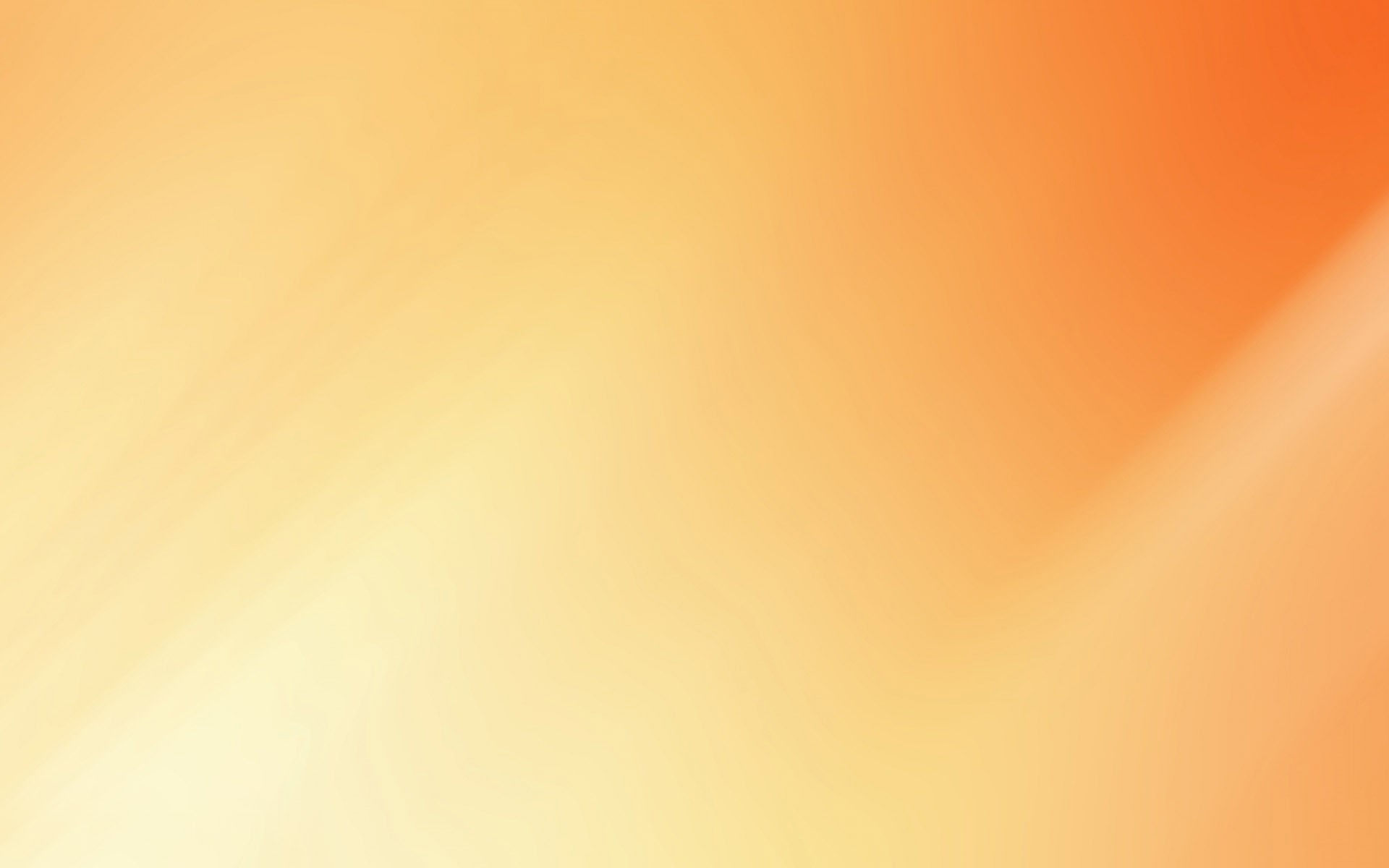
intelliPlan™
Key Solutions
Manage applicable industry specifications and guidelines (ISO, Nadcap, API, AS, TS, ITAR/EAR, MedAccred, Prime Contractors, etc.) in the part planning process to provide detailed auditability.
-
Simplify work order processing by linking quotes and work orders to current specification requirements
-
Updating specifications to a new revision is rapid and accurate everytime
-
Easily manage a single mini-process that could be used in many hundreds of other processes

intelliPlan™
Bright AM I intelliPlan™ allows the building of a sophisticated process for a new work order “on the fly” and updating a customer part process directly from the work order. The new process is built quickly and easily using the appropriate specifications and material/part processing rules to ensure higher quality of finished parts according to the required specifications.
Bright AM I intelliPlan™ leverages the power of “embedded processes” within Bright AM™. Embedded Processes are simply “mini-processes” that can be embedded within other processes. This allows you the ability to manage a single mini-process that could be used in many hundreds of other processes. When building a process on a Work Order for a new customer part, Bright AM I intelliPlan™ filters the list of possible processes to select from based on required specifications, part information and rules that you manage as part of Bluestreak I intelliPlan™. It also allows the updating/creating of a customer part process directly from the work order, saving valuable time and keystrokes.
Key Features
-
Store employee information, including their picture and individual training requirements (both safety training and production training).
-
Employee training matrices can be stored within Bluestreak™, and employees can be qualified automatically on the production floor. For example, if training is required before an employee is allowed to use a piece of equipment, Bluestreak™ will not allow them to continue processing an order if it finds their training is not completed or not current.
-
Qualify equipment. If regularly scheduled maintenance or repairs have not been completed, the equipment in question cannot be used to process an order in Bluestreak™.
-
During an internal Safety Audit, a “Concern” can be entered in Bluestreak™ along with a “CAPA – corrective and preventive action”. (Ex. Driving a forklift without wearing the seatbelt).
-
Use Bluestreak™ as an Incident Reporting System. Incident reports within a Concern, create an audit trail showing the user, date and time the incident was logged.
-
Safety Concern categories can be defined by you and set up in the system. Examples of safety categories include confined space issues, near misses, PPE (personal protective equipment) violations and damage. Because every organization faces a unique set of conditions, categories are customizable to meet your specific needs. That way, when a Safety Concern is entered into the system it can be assigned to a category.
-
Reports can be generated for all the Safety Concerns within the various categories, so you can track where the problems really are. With the largest category identified, Bluestreak™ allows the user to open a corrective action in the CAPA system to determine the root cause and eliminate the problem. The ability to link the corrective action to the concern category provides evidence that your company takes safety seriously and acts upon issues when they are discovered.
-
Everyone has the ability to enter a Safety Concern, and using Bluestreak™, anyone can enter a violation. Therefore, you may not have to use a disciplinary system unless the offense is repeat or is grave enough for that level.
-
Within Bluestreak’s™ “Phrases” capability, you can set up “Safety Violation Phrases” (or what-ever you want to call them), and within the Phrase text, you can have questions that could then be answered to capture the relevant details around an incident. This allows uniformity in how such events are managed.
-
All safety program documents can be stored within Bluestreak I Advanced Specifications Manager™, as well as scanning safety training records for each person set up in the system.
-
The Bluestreak™ “Concerns” component can be used to administrate inspection equipment that fails verification and calibration, while using the “Phrases” function to drop an “8D” problem solving template into the “Immediate Resolution” section to capture root cause, containment, actions taken, etc.
-
Bluestreak™ can also be used for external rework, using the same 8D template and the “related items” function to connect the original order and the new external rework order together in one common function.
What our users are saying
about Bright AM
“As part of our QMS we needed to manage to various industry specifications and guidelines in the Part Planning Process, while also providing detailed auditability. The Bluestreak system allows us to build a sophisticated process for a new work order on the fly and be able to update a customer part process directly from the work order, which saves us an enormous amount of time. We are also able to have embedded processes so we can easily manage a single mini process that is used in hundreds of other processes, which was a nightmare for us before. Thank you Bluestreak!”